Supporting our Clients through New Product Introduction
Systematically solving challenges that arise on the journey from design release to volume manufacturing
At Tensentric, we recognize that transitioning from design to manufacturing is a perilous time to transfer product ownership, especially in the medical field. Our ability to deliver good design for manufacturing (DFM) is enabled by design engineers’ adjacency to the manufacturing process. Owning manufacturing makes better design engineers and better designs. We support our clients’ projects through V&V and small controlled builds, to NPI and line validation and small volumes, all the way up to volume manufacturing in our FDA-registered facility because we know that having the design engineers present during the transition process improves knowledge transfer, quality and efficiency.
Fulfilling the Need for Low-Volume, High-Complexity Domestic Manufacturing for Biological Systems
Cell and gene therapy systems and medical devices aren’t always suitable for large contract manufacturers
Tensentric’s sweet spot for manufacturing is high-complexity systems which require small to medium volumes of validated products built under quality controls for initial market introduction or to support clinical trials. This makes us uniquely suited for the cell and gene therapy space, which can require high-complexity bioprocessing instruments and consumables that may never reach the volume threshold to be seriously considered by traditional large contract manufacturers, who typically prefer to wait until the product lifecycle is mature with established and consistent demand. Our manufacturing facility in Louisville, Colorado enables us to close the loop with our suppliers and clients faster to resolve any open items and get builds off the ground and processes well documented before considering a transition to low-cost offshore manufacturers.

Flexible Approach with Rigorous Process Control
Robust inspection capabilities and thoughtfully crafted quality system to meet individual client needs
To react effectively to issues that arise in manufacturing, whether due to supply chain, component qualification, or changing volume needs, our manufacturing team is set up to handle adversity with the flexibility to start and stop production and solve issues hands-on in real-time. We have incoming inspection capabilities, including a CMM and trained personnel to qualify supplier components to ensure we start on the right foot for any build. We cater to our client’s long-term manufacturing strategy; our clients own all tooling, documentation, and assembly test fixtures should they choose to transfer after scale-up and manufacturing integration issues are resolved.

WORK
WITH US
Interested in how we can help you?
Let’s chat.
Our Thinking
Clean Room Assembly of Complex Consumables
For complex consumables requiring assembly in a certified clean room, Tensentric’s experienced manufacturing team and FDA registered, ISO 13485 facility is here to help bring your product to market.
Plastic Part Tooling Strategies for Medical Device Development
Choosing a fabrication method for medical products with plastic parts carry added complexity due to the materials, precision needed, and regulatory environment.
Design for EMC Test: An Interdisciplinary Approach
Designing a medical device to meet the IEC 60601-1-2 4th edition Electromagnetic Compatibility (EMC) standards is notoriously difficult. Making matters worse, the details of what goes on during EMC...
Our Team Offerings
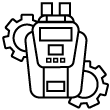
COMPLEX ELECTROMECHANICAL SYSTEMS
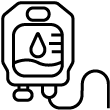
COMPLEX CONSUMABLES/ DISPOSABLES
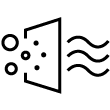
CLEANROOM ASSEMBLY
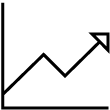
NEW PRODUCT INTRODUCTION AND RAMP TO VOLUME

SUPPLY CHAIN MANAGEMENT
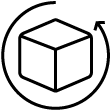
MANUFACTURING SUSTAINING
Selected Clients
We serve a broad spectrum of clients from early-stage start-ups through large and well-established medical and life sciences OEMs.
Related Insights
KEY CONSIDERATIONS FOR STERILE DEVICE DEVELOPMENT
As medical device consumables become more complex, so does manufacturing them. Sterilization is becoming an increasing concern in the industry. To ensure the proper sterilization is in place, there...
Choosing Touchscreen LCDs for your Medical Device Design
There are many features that drive LCD and touchscreen selection for a device in any industry, but these decisions become more restricted in the medical device space.
Medical Packaging Design: Thinking Outside the Box
When designing a new medical, diagnostic, or life science device, the safe and effective delivery of product is just as important as its safe and effective use. Often there are several levels of...